The Process Design and Matched Equipment Selection of Steel Grain Silo
In recent years, with the rapid development of the silo industry, the steel silo has become the preferred silo type for grain storage in grain processing plants. At first, most people think that the wall of steel silos is too thin, which will lead to large temperature differences, condensation, and other problems, to some extent, decrease the safety of grain storage. But the practice has proved that the above problems can be completely avoided by strictly controlling the moisture content of grain (generally no more than 12.5%), combining with excellent process design, and equipping with high-efficiency accessory equipment. At present, the supporting facilities in steel silos, such as grain temperature detection system, ventilation and cooling system, and circulation fumigation system provide a reliable guarantee for the safe storage of grain so that the grain is free from mildew and insect pests, keeping dry and fresh in long-term storage. Generally, as long as we meet the performance requirements of grain storage, strengthen the management, and take effective measures, the steel silo can be used as a long-term grain storage silo.Structures of Steel Silo | |
Top of the Steel Silo | Silo roof, safety guardrail, process equipment |
Middle of the Steel Silo | Silo wall, rest platform, silo gate, ladder |
Bottom of the Steel Silo | Foundation, supporting structure, silo bottom |
The Process Design of Steel Grain Silo
The process flow of grain steel silo generally includes grain loading, cleaning, measuring, unloading, ventilation, temperature measurement, material level monitoring, automatic control, etc., sometimes the fumigation process and dust removal process are also attached. Their process design should meet the requirements of saving land, reasonable cost, convenient construction, and smooth flow of conveying. We usually refer to the following principles:- The design and construction of steel grain silos should be combined with the overall planning of the factory and the geology and hydrology.
- The steel grain silos can be arranged in single or multiple rows. In exceptional cases, such as to increase the capacity of an existing silo group, staggered layouts are allowed.
- Steel silos should be designed and arranged according to the loading and unloading process of grain.
- We should shorten the distance between steel grain silos as much as possible to reduce investment and management costs.
- The process design of steel silos must meet the requirements of building construction and silo maintenance. Sufficient distance and passage should be reserved between steel silos, and the net distance can’t be less than 500 mm.
- The design of steel grain silo must meet the requirements of fire prevention, environmental protection, and safety. For areas with lightning protection requirements, related protection facilities should be added to the steel silo.
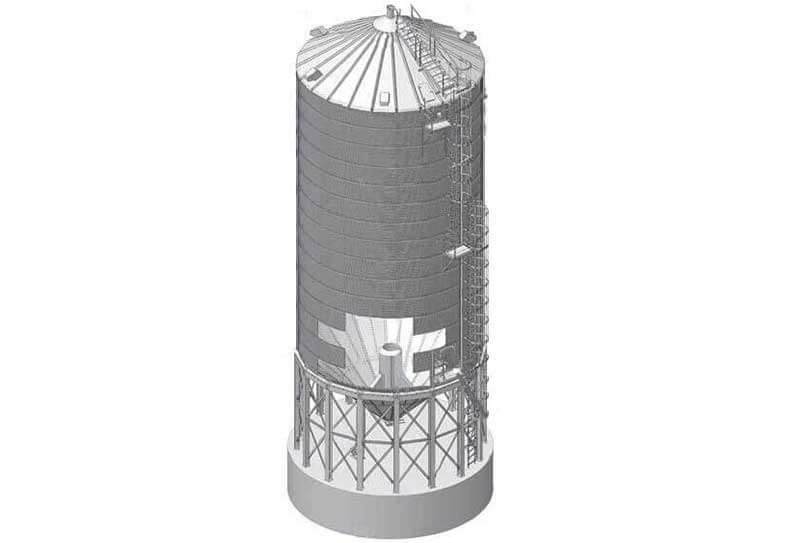
Working Tower Design
The working tower is an important part of the grain steel silo. It is equipped with mechanical equipment required by various process flows. The main task of working tower is to transport the received grain to each silo after conveying, lifting, cleaning, measurement, and dust removal. Some working towers are mounted with drying equipment to handle high moisture grain. Besides, it can also unload the grain from the silo according to requirements. The building area and height of the working tower are determined by the size and layout of selected mechanical equipment. In addition, factors such as the convenience of maintenance, loading, and unloading of the equipment should also be taken into account.
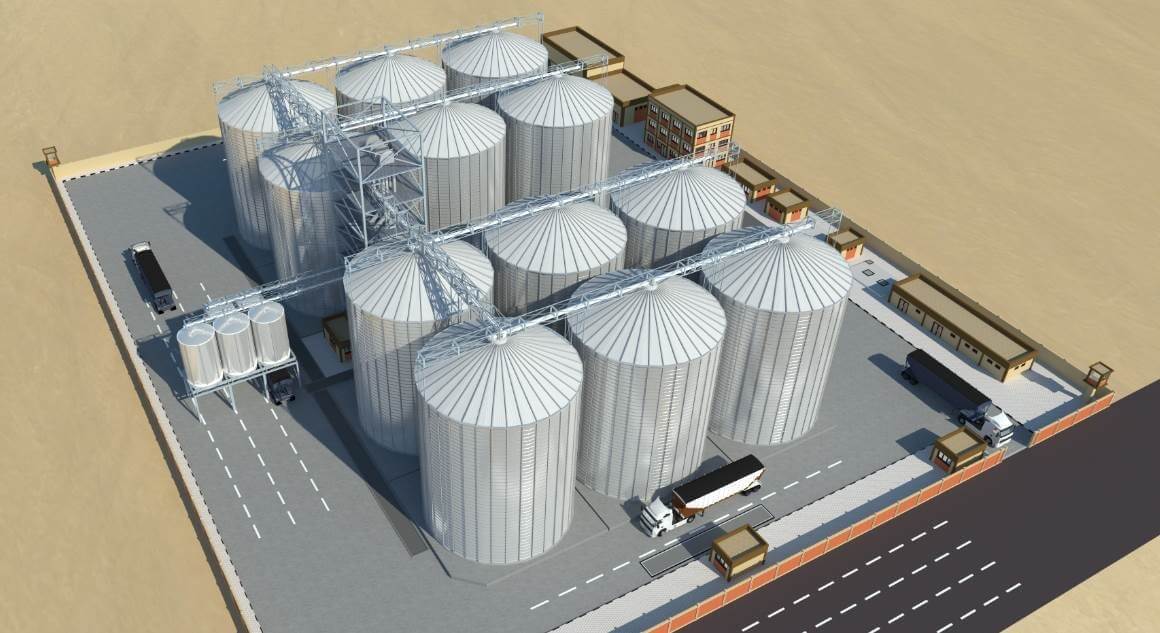
The Matched Equipment Selection of Steel Grain Silo
The selection of matched process equipment plays a decisive role in giving full play to the silo function, improving operation efficiency, saving cost, and reducing consumption. The main equipment involved includes conveying equipment, preliminary cleaning equipment, metering equipment, dust removal equipment, drying equipment, etc. How do we select the process equipment?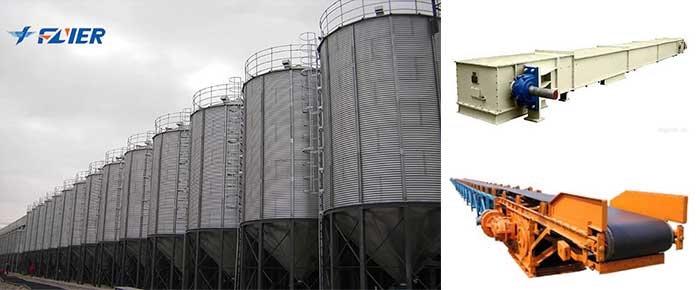
Select Equipment According to Functional Needs.
In the grain conveying system of ports and wharves, it is necessary to set up the preliminary cleaning equipment and metering equipment. While in the general grain processing enterprises, we only need the preliminary cleaning equipment. As to which type of preliminary cleaning equipment we should select, it depends on the functional need. For example, in the feed processing industry, the preliminary cleaning of corn refers to remove the corn cob, hemp rope, and other large particle impurities. While in the starch and alcohol processing industry, the preliminary cleaning not only refers to remove the above impurities but also includes smaller impurities like corn husks.
Equipment Model Selection.
In the process design of grain steel silo, en masse conveyor and belt conveyor are two frequently used devices to transport grain. The en masse conveyor can unload materials in multi-points and has good sealing performance, so it is more suitable to be applied to the top of the silo. The belt conveyor features stable operation and low material crushing ratio, suitable for long-distance transportation. For industries with high requirements for material integrity, such as the wet method starch crushing industry, belt conveyor is the best choice.
Equipment Capacity Selection.
The selection of equipment capacity depends on the capacity of the silo. If the equipment capacity is too large, it will cause the waste of investment and high operation costs. If the capacity is too small, it will lead to low operation efficiency and a long production cycle.
Get In Touch With