The Sandblasting Technology of Steel Silo
The anticorrosion treatment for the metal surfaces of steel silos usually uses the sandblasting technology. The rust removal of the metal surfaces must be accord with the Sa2 grade requirement of Rust Grades and Preparation of Steel Surfaces before Application of Paint and Related Products (GB8923-1988) of China. The metal surfaces must be cleaned after the sandblasting process. After the rust removal, the corrosion resistant construction should be performed on the metal surfaces as soon as possible. The time interval should be controlled no more than 8 hours. When the metal surface temperature is 3 ℃ lower than the exposure point or the relative humidity difference is greater than 70%, the sandblasting process is not suitable. Under the climatic conditions of rain, fog or windy weather, the related work on the construction of outdoor anti-corrosion engineering can not be carried out.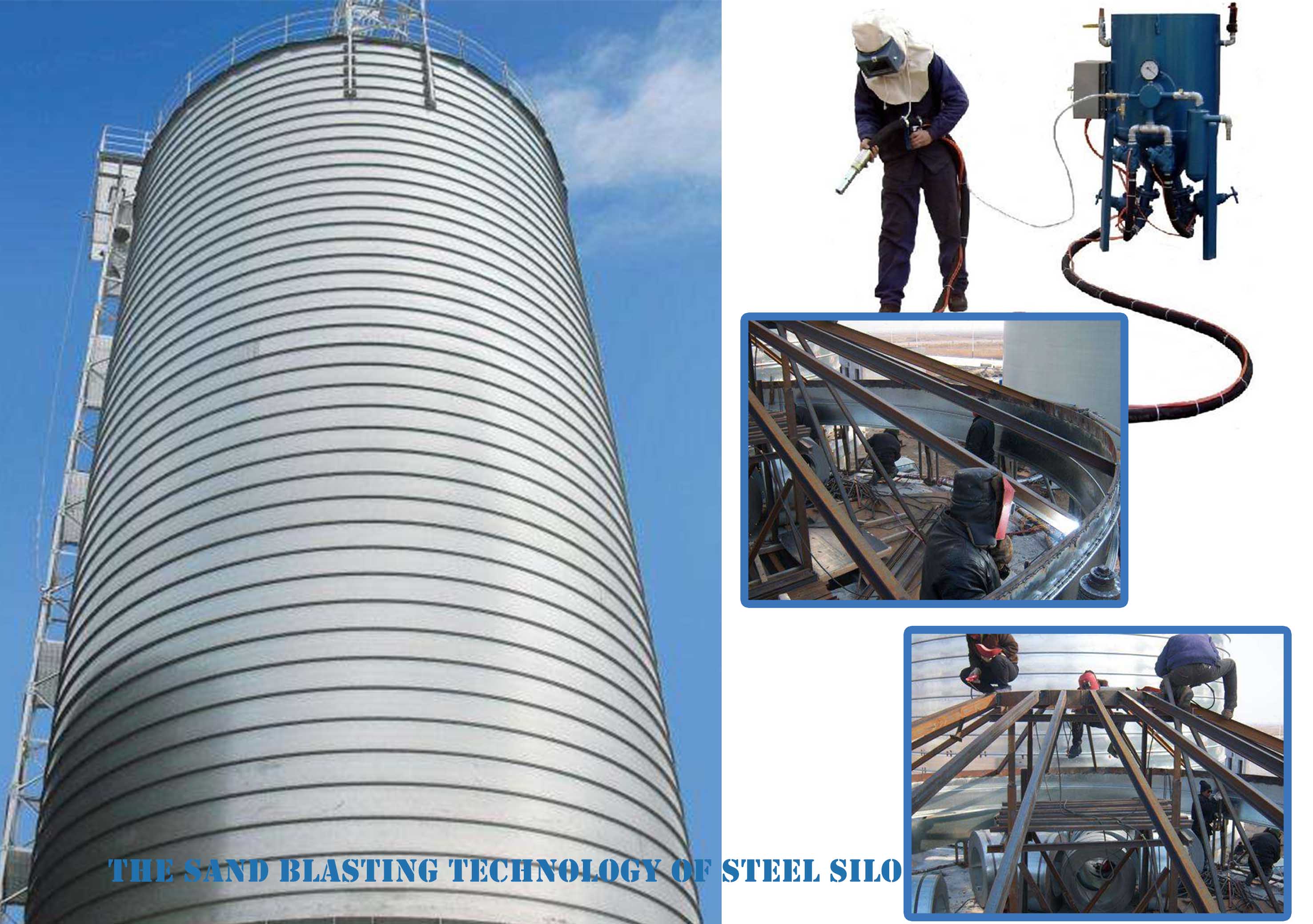
I. The anticorrosion paintings of steel silo
The preparation and application of the anticorrosion paintings must be inspected in accordance with the rules of product specifications. We should make the paintings be stirred evenly before we put them into use. They could not be used if gelling, caking or other phenomena were found in them. According to the technology requirements, the paintings must be added with the matched diluents, but the amount can not be greater than 5% of its weight.We can use construction methods of the spray method, brush painting method and roller coating method to make anti-corrosion painting. When we are using the brush painting method in construction, we need to paint from horizontal to vertical, from vertical plane to plain plane, and then from bottom to top with even force. When we are using the roller coating method, we should dip the roller first, and paint with force not too strong. For the places of the corners and the accessories, we can use the brushing method instead to get them painted.
II. The requirements for the sand blasting technology of steel silo
- The pressure of the compressed air must be maintained at 0.5-0.6Mpa, and the diameter of the spraying nozzle should be 6-8mm. When the diameter has expanded by 25%, it must be replaced.
- The welding slag, burr and welding spatter on the metal surfaces must be cleaned before the sandblasting.
- The humidity of the sandblasting treatment should be no greater than 85%, or we can’t keep the temperature of steel surfaces 3℃ higher than the air exposed points. If the humidity is too large, the steel surface and metal abrasive will get rusty easily.
- The sand material should be completely dry, no water and oil components is allowed.
- With the increasing of the sandblasting angle, the roughness value will also increase. The optimum sandblasting angle is 70-80°
- The sandblasting distance:If the hardness of the substrate surface is 45HRC or higher, the distance is required to be 100-150mm; if it is above 20HRC, the distance is required to be 150-200mm.
- The operators on site must wear windproof goggles and dust masks.
- The sandblasting treatment can be carried out from bottom to top. After spraying, we need to thoroughly clean the sand stored in all the layers of the channel steel blown from the upper layer.
III. Matters need attention for the sandblasting technology of steel silo
- Many places need to be inspected, including the cross section of the down surface of channel steel and silo wall, the welding section, each support member of the ladder, the railings and the skirting boards.
- The location of the construction section need to be checked to maintain a horizontal blast area of 200-300mm. It should be done neatly. The sandblasting treatment must be carried out carefully in this area.
- After the sandblasting treatment, examine the sprayed surface, achieving Sa2 level requirements, keep the surface clean from residue.
- The construction need to be stopped if the wind of that day is stronger than five.
- Before you begin, take full account of the impact of other types of working operations. It is important to ensure that no other operations will be affected during the sandblasting process.
FLYER Company has rich experience in designing and constructing modern large spiral steel silos. We are able to solve complex problems you may encounter. If you have any problems or requirements, please contact with us freely. We will provide you relevant specified information. We expect to build a long term partnership with you!
Get In Touch With