The Analysis Of Atmospheric Corrosion Damage On Grain Steel Silo At Early Stage Of Use
Steel silos are one of the most popular storage facilities for grain, oil, wine, feed materials and so on. Usually their service lives are between 25-30 years, but if we make wrong choice or decision in designing, material selection and maintenance, their actual service lives will be greatly shortened. It is reported that a silo had to replace some of its key parts to keep working only after a 1-year service because of improper operations. We will analysis the reasons that may cause such damages for grain steel silos and provide some effective suggestions in the following parts and we hope that this will help the users operate these facilities correctly and extend service lives of the silos.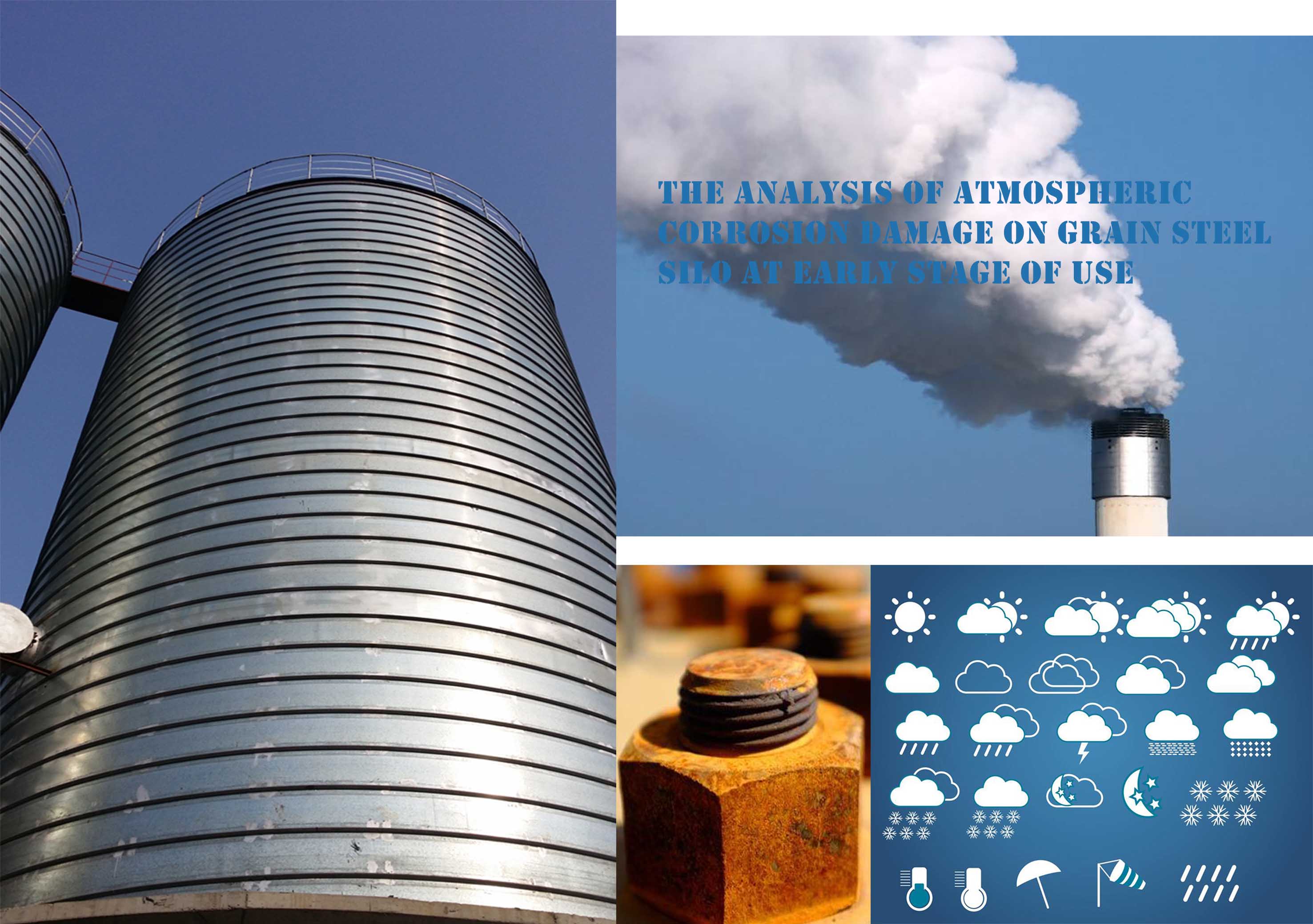
I. The reasons of corrosion damage on grain steel silos
According to reports, corrosion damages were found on some steel silos shortly after being put into use, some serious ones even had to be scrapped. Here are some possible reasons:
1. Wrong maintenance
When a lot of exposed spots on galvanized steel sheets were found on the roof of a steel silo, such as on a roof cover, the users would probably use the rusted phosphating method for surface pretreatment, that is to say they would twice take the epoxy iron red as the primer and twice take two acrylic modified alkyd resin paint as the finish. This kind of maintenance may is totally wrong because:
1) no successful precedent case can be found; 2) according to the international standards, the steel surface is required to be sand blasted to remove the residual paint and the epiphyte thoroughly. As reaching the Sa2.5 level, it can start being painted. Using the rusted phosphating method to replace sand blasting surface pretreatment, we will find that the treatment is not proper. We cannot ensure good adhesion between the paint and the metal base.
2. Wrong construction process
In construction, the surface painting cannot be performed under the rainy, snowy, icy, frost weather in winter. Between two working steps, we cannot just use a rag to wipe frequently to guarantee the thorough dryness of the surface, because it will help form suitable environmental conditions for the rapid development of the corrosion under the paint film.
3. Lack of supervision and control of the quality
A large number of real cases have shown that without the QC/QA coating, we can't provide the silo steel with sufficient protection, and this would possibly cause more severe damage.
In the interaction of the above factors, it is inevitable for us to lead to early corrosion damage of steel silo and cause some economic loss and bad social influence. So we must master the atmospheric environment adaptability of the galvanized steel sheet about steel silo.
II. The atmospheric environment adaptability of the galvanized steel sheet
The galvanized coating on the surface of the steel sheet can mainly provide two protective functions for the base metal:
A. In the case that the galvanized layer remains intact, due to its self-corrosion in the atmospheric environment, the layer will produce smaller corrosion products, for example, ZnO•xH2O or Zn (OH) Cl•yH2O and so on. They are closely attached to the surface of the layer, and usually have lower solubility in the water under the conditions of precipitation (except acid rain or alkaline pollution), which will generate huge inhibitory effect for the layer’s further dissolving
B. In those cases in which the galvanized layer is damaged in its local parts, because hot dip galvanizing or thermal spray zinc (or aluminum) galvanized layers of steel surfaces belong to the anode layers, between them and exposed spots on the surfaces of layers a zinc-iron corrosion cell will be formed when a thin water film exists. Under this condition, the galvanized layer will be a sacrificial anode to provide electrochemical protection on steel base.
The protective function of the galvanized layer and steel base is closely related to the corrosive effect of the atmospheric environment. If the atmospheric environment is determined, especially in serious corrosive environmental conditions, the service life of the protection galvanized layer will be up to the thickness of the sacrificial anode galvanized layer. For example, in the marine atmosphere with no effect of contamination, the 100μm thickness of galvanized layer can last for 20years. But in the polluted atmosphere, it can only last 10years. When the galvanized layer is only 24μm, in the clear marine atmosphere, the service life of the layer can reach 4-5 years, but in the polluted atmosphere, it can only reach 2 years. If the galvanized steel sheets are in poor quality, the effective protection period will be further shortened. If the protective service life of the galvanized layer was supposed to reach 10 years, its thickness should at least be 100μm.
III. Protection measures
1. The overall design according to local conditions
In the overall design of the structure strength of new steel silos, we must confirm the silos’ corrosion resistance of local atmospheric environment and their service life, this process includes proper material selection, anticorrosion design of rainwater guiding channel, the surface protection and local reinforcement of the fastening bolts and nuts.
2. Select proper materials
We have to select materials properly to make the steel silo reach a longer service life. To obtain more suitable application, the basic structural materials we choose must be corresponded to the thickness of the galvanized layer.
3. Correct construction
During the processes of factory prefabrication, transportation, installation, and construction, we must try our best to avoid the scratches on the surfaces of galvanized steel sheets, particularly the damages on a wide area of the exposed iron.
4. Local reinforcement
The aim of local reinforcement is to protect the parts that is lack of protection in the overall structure, such as the welding zone, bolts, nuts and so on.
In summary, the key to make steel silos, especially those in corrosive atmospheric environment, have a long service life and low maintenance cost is the corrosion protection. We must do our best in the overall design, material selection and each step of construction, and take a series of technical measures to ensure high quality of steel silos.
Get In Touch With